- Chintamani Stainless Inc, 132, T.P. Streets, 6th Kumbharwada Lane, Mumbai- 400004, India
- Trophy Winning
- Ceritified ( ISO 9005-2010 )
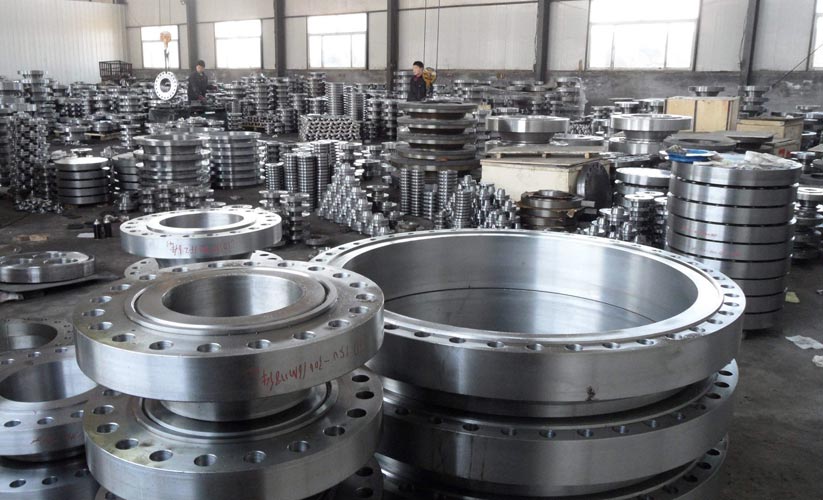
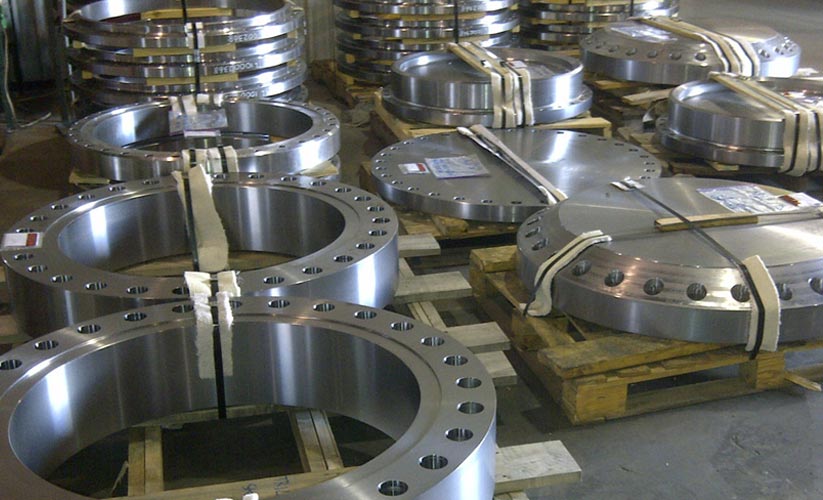
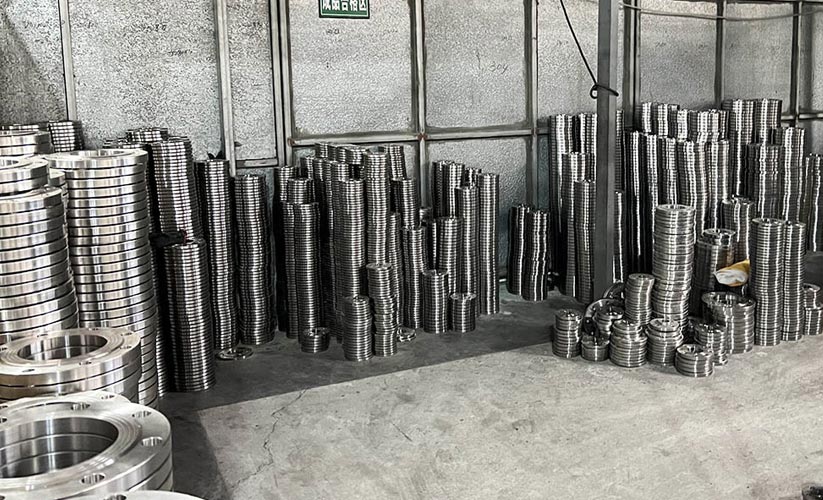
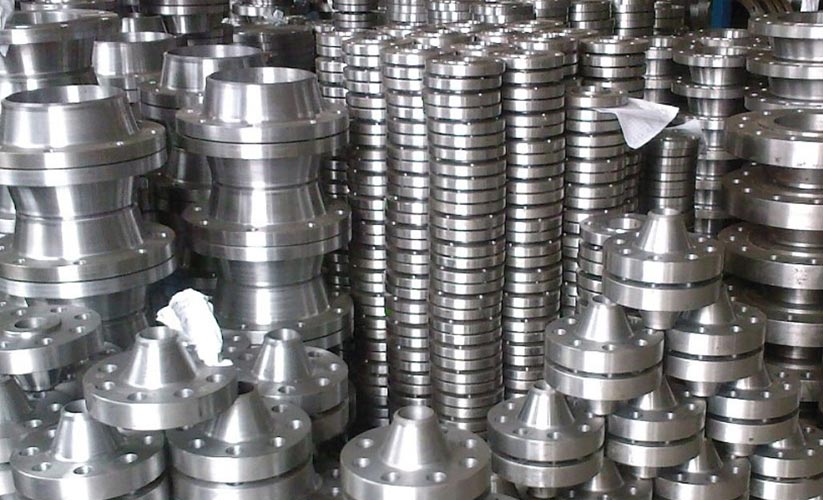
Duplex flanges
Chintamani Stainless Incs is well-known supplier, manufacturer and exporter of Duplex S31083 / S32205 Flanges with high quality raw materials. We follow long procedure of Duplex Steel UNS S31803 Blind Flanges quality control, under which we carefully assess all our products on the basis of quality parameters. Our offered ASME SA182 Duplex Steel UNS S32205 Weld Neck Flanges are supply to sea water and power generation equipment as their smooth surfaces can endure a temperature up to 600 ° F besides promoting excellent flow characteristics.
Duplex Steel DIN 1.4462 Socket Weld Flanges demonstrate good fatigue strength, as well as outstanding resistance to stress corrosion cracking, crevice, pitting, erosion, and general corrosion in severe environments. As a referred stockholder we have huge inventory of Duplex Steel ASTM A182 Flanges include Duplex Steel S31803 Weld Neck Flanges, Duplex 2205 Slip On Flanges, Duplex F51 Socket Weld Flanges,Duplex Steel F56 Orifice Flanges, Gr. F52 Duplex Blind Flanges, Duplex Steel S32205 Spectacle Blind Flanges, Duplex Steel F60 Screwed / Threaded Flanges, Duplex 2205 Ring Type Joint Flanges (RTJ), Duplex Steel F61 Reducing Flanges etc.
The 2205 Duplex Steel consists of a two-phase microstructure, which is ferritic and austenitic. Talking
about the chemical composition of 2205 Duplex Steel Flanges, they mainly contain 22% chromium, 3%
molybdenum, and 5-6% nickel, present in the form of alloyed stainless steel. We are one of the top
Duplex Steel Flanges Manufacturers In India who produces different types of flanges of the given grade
according to the needs of our clients. As a result, we have a good stock of various Duplex Stainless
Steel Flanges, known for their high yield strength- almost double than the standard austenitic stainless
steel grade.
We are one of the biggest producers of Duplex Steel Slip On Flanges that have good fatigue strength and
are highly resistive to corrosion. The 2205 Duplex Steel Blind Flange is also known for its various
mechanical properties, such as excellent resistance to cracking, pitting, erosion, and that too in
severe environments. Our high-quality Duplex Weld Neck Flanges have applications in various industries
like chemical, transportation, and storage. We are amongst the biggest stockists of ASTM A182 Duplex
Steel Threaded Flanges in India, which possess good weldable properties. All of our products are
supplied to different parts of the world, and we have many happy clients. We offer product delivery to
your doorstep.
Flanges constructed from UNS S32205, also called Duplex 2205, possess remarkable attributes derived from
their distinct composition. These duplex stainless steel components are made from a 50/50 blend of
ferrite and austenite, giving them a dual-phase structure that confers various beneficial
characteristics.
Foremost among these is an extraordinary corrosion resistance. The flanges' chemical composition, which
includes substantial quantities of chromium, molybdenum, and nitrogen, fosters the formation of a
protective layer on their surface. This shields the flanges from various corrosion types, including
general, pitting, crevice corrosion, and stress corrosion cracking.
Specification List Of Duplex Flanges
Standards Specification Of : | Duplex Steel Flanges |
---|---|
Manufacturing Shapes | RTJ,FF, Raised Face, Lap-Joint Face, Large Tongue & Groove And Small Tongue Groove, Large Male-Female And Small Male-Female |
Size Chart | 1/2" to 48" |
High Temperature Of Flanges | Above 200°C (400°F) For 150LB Or Above 400°C (750°F) |
Low Temperature Of Flanges | Above -29 °C (−20°F) |
Japanese Standards | 5K, 10 K, 40 K, 16 K 20 K 30 K, 63 K |
Materials | Stainless Steel, Carbon Steel, Inconel, Hastelloy, Copper Nickel, Cast Iron, Alloy Steel, Mild Steel, Duplex Steel & Super Duplex Steel, Wrought Iron. |
Flanges Thickness | NPS ≤ 18 |
Bore Diameter Of Flange | NPS ≤ 10 |
Flanges Standards | MSS S44, ISO70051, ASME B16.36, DIN, BS1560-3.1, API7S-15, API, ISO, UNI, EN-1092, ANSI/ASME B16.5, B16.47 Series A & B, ASME B16.48, AWWA C207, IS 2062, EN1092, API7S-43, API605, BS4504 |
ASME B16.5 Ratings | 150, 300, 400, 600, 900, 1500, 2500 |
Production technique |
|
Most common types | Threaded / Screwed / Forged / Plate |
ASME & ANSI Flange Types | Slip-On, Weld Neck, Blind, Lap Joint, Threaded, Socket-Weld |
Industries Use Flanges | Municipal & Waterworks Pipe Systems Food Processing & Manufacturing Power Plants And The Nuclear Power Industry |
Equivalent Grade Of SAF 2205 Duplex Stainless Steel
STANDARD | WERKSTOFF NR. | UNS |
2205 Duplex Steel Flanges | 1.4462 | UNS S31803 Flanges/ UNS S32205 Flanges |
ASME B16.5-2013 | ASME B16.47-2011 | MSS SP-44-2010 |
EN 1092-1-2007 | EN 1759-1-2004 | ISO 7005-1-1992 |
GB/T 9112-2010 | GB/T 9123-2010 | AS 2129-2000 |
HG/T 20592-2009 | HG/T 20615-2009 | HG/T 20623-2009 |
SH/T 3406-2013 | GOST- AFNOR- BS- DIN | - |
European Series | American Series |
---|---|
Type B (Raised Face) | Raised Face (RF) |
Type A (Flat Face) | Flat Face (FF) |
Type G (O-Ring Spigot) | Ring Joints Face (RJ) |
Type D (Groove) | Groove (G) |
Type C(Tongue) | Tongue (T) |
Type F (Recess) | Male (M) |
Type E (Spigot) | Female (F) |
Type H (O-Ring Groove) | - |
Duplex 2205/UNS S3205 / UNS31803 / EN 1.4462 Blind Flanges Dimensions Chart
Normal Pipe Size (NPS) | Outside Daimeter (O.D.) Of Flange | Thickness Of Flanges | Diameter of Raised Face | Hub at Base Diameter | Lengtd Tdru Hub | Bore And Diameter | Hub at Bevel Diameter | Radius of Fillet | Socket Deptd | |||
---|---|---|---|---|---|---|---|---|---|---|---|---|
Weld Neck (WN) | SORF (Slip-On) NPT (Threaded) SWRF (Socket) | Loose (Lap Joint) | SORF (Slip-on) SWRF (Socket) | Loose (Lap Joint) | ||||||||
O | Q | R | X | Y | Y | Y | W | B | H | r | Z | |
1/2 | 3-1/2 | 7/16 | 1-3/8 | 1-3/16 | 1-7/8 | 5/8 | 5/8 | .88 | .90 | .84 | 1/8 | 3/8 |
3/4 | 3-7/8 | 1/2 | 1-11/16 | 1-1/2 | 2-1/16 | 5/8 | 5/8 | 1.09 | 1.11 | 1.05 | 1/8 | 7/16 |
1 | 4-1/4 | 9/16 | 2 | 1-15/16 | 2-3/16 | 11/16 | 11/16 | 1.36 | 1.38 | 1.32 | 1/8 | 1/2 |
1-1/4 | 4-5/8 | 5/8 | 2-1/2 | 2-5/16 | 2-1/4 | 13/16 | 13/16 | 1.70 | 1.72 | 1.66 | 3/16 | 9/16 |
1-1/2 | 5 | 11/16 | 2-7/8 | 2-9/16 | 2-7/16 | 7/8 | 7/8 | 1.95 | 1.97 | 1.90 | 1/4 | 5/8 |
2 | 6 | 3/4 | 3-5/8 | 3-1/16 | 2-1/2 | 1 | 1 | 2.44 | 2.46 | 2.38 | 5/16 | 11/16 |
2-1/2 | 7 | 7/8 | 4-1/8 | 3-9/16 | 2-3/4 | 1-1/8 | 1-1/8 | 2.94 | 2.97 | 2.88 | 5/16 | 3/4 |
3 | 7-1/2 | 15/16 | 5 | 4-1/4 | 2-3/4 | 1-3/16 | 1-3/16 | 3.57 | 3.60 | 3.50 | 3/8 | 13/16 |
3-1/2 | 8-1/2 | 15/16 | 5-1/2 | 4-13/16 | 2-13/16 | 1-1/4 | 1-1/4 | 4.07 | 4.10 | 4.00 | 3/8 | 7/8 |
4 | 9 | 15/16 | 6-3/16 | 5-5/16 | 3 | 1-5/16 | 1-5/16 | 4.57 | 4.60 | 4.50 | 7/16 | 15/16 |
5 | 10 | 15/16 | 7.5/16 | 6-7/16 | 3-1/2 | 1-7/16 | 1-7/16 | 5.66 | 5.69 | 5.56 | 7/16 | 15/16 |
6 | 11 | 1 | 8-1/2 | 7-9/16 | 3-1/2 | 1-9/16 | 1-9/16 | 6.72 | 6.75 | 6.63 | 1/2 | 1-1/16 |
8 | 13-1/2 | 1-1/8 | 10-5/8 | 9-11/16 | 4 | 1-3/4 | 1-3/4 | 8.72 | 8.75 | 8.63 | 1/2 | 1-1/4 |
10 | 16 | 1-3/16 | 12-3/4 | 12 | 4 | 1-15/16 | 1-15/16 | 10.88 | 10.92 | 10.75 | 1/2 | 1-5/16 |
12 | 19 | 1-1/4 | 15 | 14-3/8 | 4-1/2 | 2-3/16 | 2-3/16 | 12.88 | 12.92 | 12.75 | 1/2 | 1-9/16 |
14 | 21 | 1-3/8 | 16-1/4 | 15-3/4 | 5 | 2-1/4 | 3-1/8 | 14.14 | 14.18 | 14.00 | 1/2 | 1-5/8 |
16 | 23-1/2 | 1-7/16 | 18-1/2 | 18 | 5 | 2-1/2 | 3-7/16 | 16.16 | 16.19 | 16.00 | 1/2 | 1-3/4 |
18 | 25 | 1-9/16 | 21 | 19-7/8 | 5-1/2 | 2-11/16 | 3-13/16 | 18.18 | 18.20 | 18.00 | 1/2 | 1-15/16 |
20 | 27-1/2 | 1-11/16 | 23 | 22 | 5-11/16 | 2-7/8 | 4-1/16 | 20.20 | 20.25 | 20.00 | 1/2 | 2-1/8 |
24 | 32 | 1-7/8 | 27-1/4 | 26-1/8 | 6 | 3-1/4 | 4-3/8 | 24.25 | 24.25 | 24.00 | 1/2 | 2-1/2 |
Duplex Stainless Steel Flange Pressure Rating
2205 Duplex Steel Flanges | Pressure And Temperature Ratings | ||||||
Temperature °F | Class 150 As Per ASME B16.5 | Class 300 As Per ASME B16.5 | Class 400 As Per ASME B16.5 | Class 600 As Per ASME B16.5 | Class 900 As Per ASME B16.5 | Class 1500 As Per ASME B16.5 | Class 2500 As Per ASME B16.5 |
-20 to 100 | 275 | 720 | 960 | 1440 | 2160 | 3600 | 6000 |
200 | 230 | 600 | 800 | 1200 | 1800 | 3000 | 5000 |
300 | 205 | 540 | 720 | 1080 | 1620 | 2700 | 4500 |
400 | 190 | 495 | 660 | 995 | 1490 | 2485 | 4140 |
500 | 170 | 465 | 620 | 930 | 1395 | 2330 | 3880 |
600 | 140 | 435 | 580 | 875 | 1310 | 2185 | 3640 |
650 | 125 | 430 | 575 | 860 | 1290 | 2150 | 3580 |
700 | 110 | 425 | 565 | 850 | 1275 | 2125 | 3540 |
750 | 95 | 415 | 555 | 830 | 1245 | 2075 | 3460 |
800 | 80 | 405 | 540 | 805 | 1210 | 2015 | 3360 |
850 | 65 | 395 | 530 | 790 | 1190 | 1980 | 3300 |
900 | 50 | 390 | 520 | 780 | 1165 | 1945 | 3240 |
950 | 35 | 380 | 510 | 765 | 1145 | 1910 | 3180 |
1000 | 20 | 320 | 430 | 640 | 965 | 1605 | 2675 |
1050 | 20 | 310 | 410 | 615 | 925 | 1545 | 2570 |
1100 | 20 | 255 | 345 | 515 | 770 | 1285 | 2145 |
1150 | 20 | 200 | 265 | 400 | 595 | 995 | 1655 |
1200 | 20 | 155 | 205 | 310 | 465 | 770 | 1285 |
1250 | 20 | 115 | 150 | 225 | 340 | 565 | 945 |
1300 | 20 | 85 | 115 | 170 | 255 | 430 | 715 |
1350 | 20 | 60 | 80 | 125 | 185 | 310 | 515 |
1400 | 20 | 50 | 65 | 95 | 145 | 240 | 400 |
1450 | 15 | 35 | 45 | 70 | 105 | 170 | 285 |
1500 | 10 | 25 | 35 | 55 | 80 | 135 | 230 |
ASTM A182 Duplex Steel 2205 Flanges Schedule Chart
NPS (Nominal Pipe Size) | SORF (Slip On) | NPT (Threaded) | SWRF (Socket Weld) | Loose (Lap Joint) | BLRF (Blind) | WRNR (Weld Neck) |
---|---|---|---|---|---|---|
½ | 1 | 1 | 2 | 1 | 2 | 2 |
¾ | 2 | 2 | 2 | 2 | 2 | 2 |
1 | 2 | 2 | 2 | 2 | 2 | 3 |
1¼ | 3 | 3 | 3 | 3 | 3 | 3 |
1½ | 3 | 3 | 3 | 3 | 4 | 4 |
2 | 5 | 5 | 5 | 5 | 5 | 6 |
2½ | 8 | 8 | 8 | 8 | 7 | 10 |
3 | 9 | 9 | 9 | 9 | 9 | 11.5 |
3½ | 11 | 12 | 11 | 11 | 13 | 12 |
4 | 13 | 13 | 13 | 13 | 17 | 16.5 |
5 | 15 | 15 | 15 | 15 | 20 | 21 |
6 | 19 | 19 | 19 | 19 | 27 | 26 |
8 | 30 | 30 | 30 | 30 | 47 | 42 |
10 | 43 | 43 | 43 | 43 | 70 | 54 |
12 | 64 | 64 | 64 | 64 | 123 | 88 |
14 | 90 | 90 | 90 | 105 | 140 | 114 |
16 | 106 | 98 | 98 | 140 | 180 | 140 |
18 | 130 | 130 | 130 | 160 | 220 | 165 |
20 | 165 | 165 | 165 | 195 | 285 | 197 |
22 | 185 | 185 | 185 | 245 | 355 | 225 |
24 | 220 | 220 | 220 | 275 | 430 | 268 |
Duplex Stainless Steel Flanges Size Chart
Normal Sizes In inch | Dimension | ASME B16.5 2205 Duplex Steel Flanges Dimensional Sizes 1/2 inch. to 2 1/2 inch. | ||||||||||||||
---|---|---|---|---|---|---|---|---|---|---|---|---|---|---|---|---|
Class 125 Class 150 |
Class 300 | Class 400 | Class 600 | Class 900 | Class 1500 | Class 2500 | ||||||||||
inch. | mm | inch. | millimeter | inch. | mm | inch. | mm | inch. | mm | inch. | mm | inch | mm | |||
1/2 | A | 3 1/2 | 88.9 | 3 3/4 | 95.2 | 3 3/4 | 95.2 | 3 3/4 | 95.2 | 4 3/4 | 121 | 4 3/4 | 121 | 5 1/4 | 133.4 | |
b | 7/16 | 11.1 | 9/16 | 14.3 | 9/16 | 14.3 | 9/16 | 14.3 | 7/8 | 22.2 | 7/8 | 22.2 | 1 3/16 | 30.2 | ||
D2 | 1 3/8 | 34.9 | 1 3/8 | 34.9 | 1 3/8 | 34.9 | 1 3/8 | 34.9 | 1 3/8 | 34.9 | 1 3/8 | 34.9 | 1 3/8 | 34.9 | ||
D1 | 2 3/8 | 60.3 | 2 5/8 | 66.7 | 2 5/8 | 66.7 | 2 5/8 | 66.7 | 3 1/4 | 82.6 | 3 1/4 | 82.6 | 3 1/2 | 88.9 | ||
n | 4 | 4 | 4 | 4 | 4 | 4 | 4 | 4 | 4 | 4 | 4 | - | 4 | 44 | ||
d | 5/8 | 15.9 | 5/8 | 15.9 | 5/8 | 15.9 | 5/8 | 15.9 | 7/8 | 22.2 | 7/8 | 22.2 | 7/8 | 22.2 | ||
3/4 | A | 3 7/8 | 98.4 | 4 5/8 | 117.5 | 4 5/8 | 117.5 | 4 5/8 | 117.5 | 5 1/8 | 130 | 5 1/8 | 130 | 5 1/2 | 139.7 | |
b | 1/2 | 12.7 | 5/8 | 15.9 | 5/8 | 15.9 | 5/8 | 15.9 | 1 | 25.4 | 1 | 25.4 | 1 1/4 | 31.8 | ||
D2 | 1 11/16 | 42.9 | 1 11/16 | 42.9 | 1 11/16 | 42.9 | 1 11/16 | 42.9 | 1 11/16 | 42.9 | 1 11/16 | 42.9 | 1 11/16 | 42.9 | ||
D1 | 2 3/4 | 69.8 | 3 1/4 | 82.5 | 3 1/4 | 82.5 | 3 1/4 | 82.5 | 3 1/2 | 88.9 | 3 1/2 | 88.9 | 3 3/4 | 95.2 | ||
n | 4 | 4 | 4 | 4 | 4 | 4 | 4 | 4 | 4 | 4 | 4 | - | 4 | 44 | ||
d | 5/8 | 15.9 | 3/4 | 19 | 3/4 | 19 | 3/4 | 19 | 7/8 | 22.2 | 7/8 | 22.2 | 7/8 | 22.2 | ||
1 | A | 4 1/4 | 108 | 4 7/8 | 123.8 | 4 7/8 | 123.8 | 4 7/8 | 123.8 | 5 7/8 | 149.2 | 5 7/8 | 149.2 | 6 1/4 | 159 | |
b | 9/16 | 14.3 | 11/16 | 17.5 | 11/16 | 17.5 | 11/16 | 17.5 | 1 1/8 | 28.6 | 1 1/8 | 28.6 | 1 3/8 | 34.9 | ||
D2 | 2 | 50.8 | 2 | 50.8 | 2 | 50.8 | 2 | 50.8 | 2 | 50.8 | 2 | 50.8 | 2 | 50.8 | ||
D1 | 3 1/8 | 79.4 | 3 1/2 | 88.9 | 3 1/2 | 88.9 | 3 1/2 | 88.9 | 4 | 102 | 4 | 102 | 4 1/4 | 108 | ||
n | 4 | 4 | 4 | 4 | 4 | 4 | 4 | 4 | 4 | 4 | 4 | 4 | 4 | 4 | ||
d | 5/8 | 15.9 | 3/4 | 19 | 3/4 | 19 | 3/4 | 19 | 1 | 25.4 | 1 | 25.4 | 1 | 25.4 | ||
1 1/4 | A | 4 5/8 | 117.5 | 5 1/4 | 133.4 | 5 1/4 | 133.4 | 5 1/4 | 133.4 | 6 1/4 | 159 | 6 1/4 | 159 | 7 1/4 | 184.2 | |
b | 5/8 | 15.9 | 3/4 | 19 | 13/16 | 20.6 | 13/16 | 20.6 | 1 1/8 | 28.6 | 1 1/8 | 28.6 | 1 1/2 | 38.1 | ||
D2 | 2 1/2 | 63.5 | 2 1/2 | 63.5 | 2 1/2 | 63.5 | 2 1/2 | 63.5 | 2 1/2 | 63.5 | 2 1/2 | 63.5 | 2 1/2 | 63.5 | ||
D1 | 3 1/2 | 88.9 | 3 7/8 | 98.4 | 3 7/8 | 98.4 | 3 7/8 | 98.4 | 4 3/8 | 111 | 4 3/8 | 111 | 5 1/8 | 130 | ||
n | 4 | 4 | 4 | 4 | 4 | 4 | 4 | 4 | 4 | 4 | 4 | 4 | 4 | 4 | ||
d | 5/8 | 15.9 | 3/4 | 19 | 3/4 | 19 | 3/4 | 19 | 1 | 25.4 | 1 | 25.4 | 1 1/8 | 28.6 | ||
1 1/2 | A | 5 | 127 | 6 1/8 | 155.6 | 6 1/8 | 155.6 | 6 1/8 | 155.6 | 7 | 177.8 | 7 | 177.8 | 8 | 203 | |
b | 11/16 | 17.5 | 13/16 | 20.6 | 7/8 | 22.2 | 7/8 | 22.2 | 1 1/4 | 31.8 | 1 1/4 | 31.8 | 1 3/4 | 44.5 | ||
D2 | 2 7/8 | 73 98 | 2 7/8 | 73 | 2 7/8 | 73 | 2 7/8 | 73 | 2 7/8 | 73 | 2 7/8 | 73 | 2 7/8 | 73 | ||
D1 | 3 7/8 | 4 | 4 1/2 | 114 | 4 1/2 | 114 | 4 1/2 | 114 | 4 7/8 | 124 | 4 7/8 | 124 | 5 3/4 | 146 | ||
n | 4 | 4 | 4 | 4 | 4 | 4 | 4 | 4 | 4 | 4 | 4 | 4 | 4 | 4 | ||
d | 5/8 | . 15.9 | 7/8 | 22.2 | 7/8 | 22.2 | 7/8 | 22.2 | 1 1/8 | 28.6 | 1 1/8 | 28.6 | 1 1/4 | 31.8 | ||
2 | A | 6 | 152.4 | 6 1/2 | 165.1 | 6 1/2 | 165.1 | 6 1/2 | 165.1 | 8 1/2 | 215.9 | 8 1/2 | 215.9 | 9 1/4 | 234.9 | |
b | 3/4 | 19 | 7/8 | 22.2 | 1 | 25.4 | 1 | 25.4 | 1 1/2 | 38.1 | 1 1/2 | 38.1 | 2 | 50.8 | ||
D2 | 3 5/8 | 92.1 | 3 5/8 | 92.1 | 3 5/8 | 92.1 | 3 5/8 | 92.1 | 3 5/8 | 92.1 | 3 5/8 | 92.1 | 3 5/8 | 92.1 | ||
D1 | 4 3/4 | 121 | 5 | 127 | 5 | 127 | 5 | 127 | 6 1/2 | 165.1 | 6 1/2 | 165.1 | 6 3/4 | 171 | ||
n | 4 | 4 | 8 | 8 | 8 | 8 | 8 | 8 | 8 | 8 | 8 | 8 | 8 | 8 | ||
d | 3/4 | 19 | 3/4 | 19 | 3/4 | 19 | 3/4 | 19 | 1 | 25.4 | 1 | 25.4 | 1 1/8 | 28.6 | ||
2 1/2 | A | 7 | 177.8 | 7 1/2 | 190.5 | 7 1/2 | 190.5 | 7 1/2 | 190.5 | 9 5/8 | 244 | 9 5/8 | 244 | 10 1/2 | 266.7 | |
b | 7/8 | 22.2 | 1 | 25.4 | 1 1/8 | 28.6 | 1 1/8 | 28.6 | 1 5/8 | 41.3 | 1 5/8 | 41.3 | 2 1/4 | 57.2 | ||
D2 | 4 1/8 | 104.8 | 4 1/8 | 104.8 | 4 1/8 | 104.8 | 4 1/8 | 104.8 | 4 1/8 | 105 | 4 1/8 | 105 | 4 1/8 | 105 | ||
D1 | 5 1/2 | 139.7 | 5 7/8 | 149.2 | 5 7/8 | 149.2 | 5 7/8 | 149.2 | 7 1/2 | 190.5 | 7 1/2 | 190.5 | 7 3/4 | 197 | ||
n | 4 | 4 | 8 | 8 | 8 | 8 | 8 | 8 | 8 | 8 | 8 | 8 | 8 | 8 | ||
d | 3/4 | 19 | 7/8 | 22.2 | 7/8 | 22.2 | 7/8 | 22.2 | 1 1/8 | 28.6 | 1 1/8 | 28.6 | 1 1/4 | 31.8 |
Duplex 2205/UNS S3205 / UNS31803 / EN 1.4462 Flange Chemical Composition
Grade | N | Mn | Si | C | S | P | Mo | Cr | Ni | Fe |
S32205 | 0.8 – 0.20 | 2.00 max | 1.00 max | 0.030 max | 0.020 max | 0.030 max | 2.50 - 3.50 | 21.0 – 23.0 | 4.50 – 6.50 | 63.54 min |
S31803 | 0.14 – 0.20 | 2.00 max | 1.00 max | 0.030 max | 0.020 max | 0.030 max | 3.0 – 3.5 | 22.0 – 23.0 | 4.50 – 6.50 | 63.72 min |
Mechanical Properties Of DDuplex 2205/UNS S3205 / UNS31803 / EN 1.4462 Flange
Grades | Melting Point (°F) | Density (lb/in 3) | Density (g/cm 3) | Melting Point (°C) |
S31803 / S32205 | 2588 – 2669 | 0.285 | 7.805 | 1420 – 1465 |
General characteristics
Steel designations |
Performance |
Typical chemical composition, % by mass |
||||||||||
name |
EN |
ASTM |
UNS |
PRE |
A1) |
Rp0.2 |
Grade |
C |
Cr |
Ni |
Mo |
N |
2205 | 1.4462 | 2205 | S32205 | 35 | 20 | 500 | D | 0.02 | 22.4 | 5.7 | 3.1 | 0.17 |
2507 | 1.4410 | 2507 | S32750 | 43 | 20 | 550 | D | 0.02 | 25.0 | 7.0 | 4.0 | 0.27 |
2205 stainless steel grades | Industry Specifications | UNS |
Duplex 2205 2205 (EN 1.4462/UNS S32205 & S31803) |
• Cargo tanks in chemical tankers • Pulp and paper industry applications such as digesters and process tanks • Oil and gas industry, typically tubular products, flanges, fittings and valves • Structural components in bridges |
• Cold rolled coil and sheet • Hot rolled coil and sheet • Quarto plate • Bar • Wire rod • Semi-finished (bloom, billet, ingot & slab) |
Duplex 2507 2507 (EN 1.4410/UNS S32750) A super duplex product with higher corrosion resistance and mechanical strength than Forta DX 2205. Often used in extremely corrosive environments. |
• Desalination plants • Industrial piping • Scrubbers • Oil and gas industry, typically tubular products, flanges,fittings and valves • Deep-sea pipelines |
• Cold rolled coil and sheet • Hot rolled coil and sheet • Quarto plate • Bar • Wire rod • Semi-finished (bloom, billet, ingot & slab) |
Duplex 32760 100 (EN 1.4501/UNS S32760) A super duplex product with higher corrosion resistance and mechanical strength than Forta DX 2205. Often used in extremely corrosive environments. |
• Desalination plants • Industrial piping • Scrubbers • Oil and gas industry, typically tubular products, flanges, fittings and valves • Deep-sea pipelines |
• Cold rolled coil and sheet • Hot rolled coil and sheet • Quarto plate • Bar • Wire rod • Semi-finished (bloom, billet, ingot & slab) |
Performance
Elongation vs. corrosion resistance.
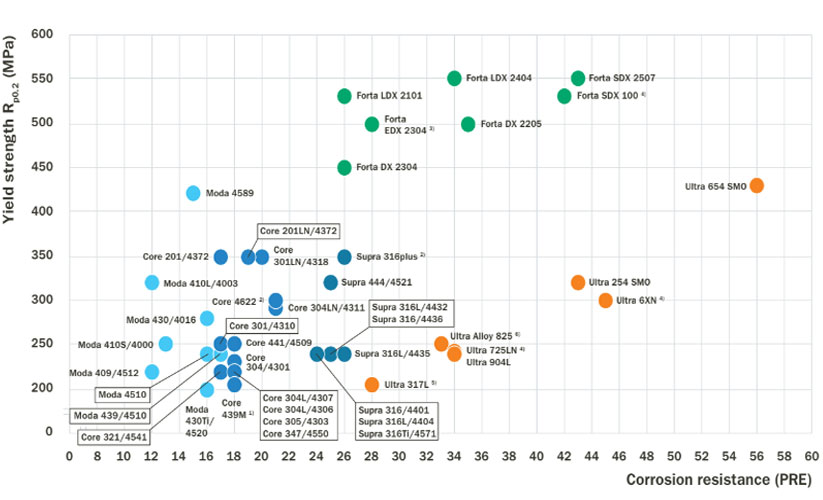
Elongation vs. Corrosion resistance
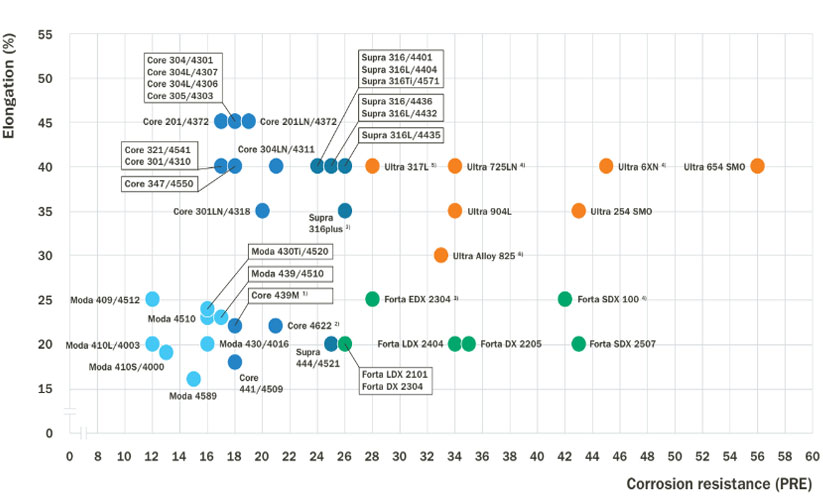
Strength vs. Corrosion resistance
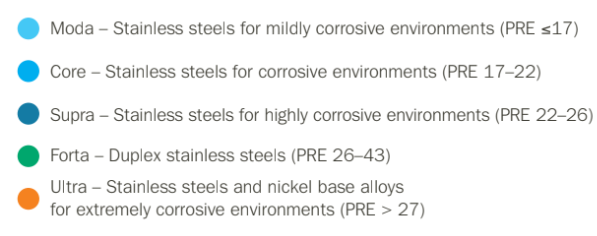
Elongation vs. Corrosion resistance
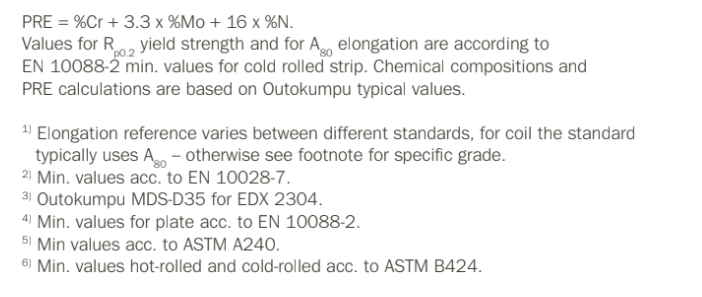
Duplex stainless steels, known for their high chromium content, provide excellent corrosion resistance, particularly in uniform corrosion environments with rates below 0.1 mm/year. Forta DX 2205 shows superior resistance to chloride-contaminated sulfuric acid compared to traditional stainless steels like Supra 316L/4404, approaching the performance of Ultra 904L. In dilute hydrochloric acid, Forta SDX 2507 and similar high-alloyed duplex steels are suitable, though localized corrosion risks exist around crevices even within safe usage limits.
Corrosion resistance
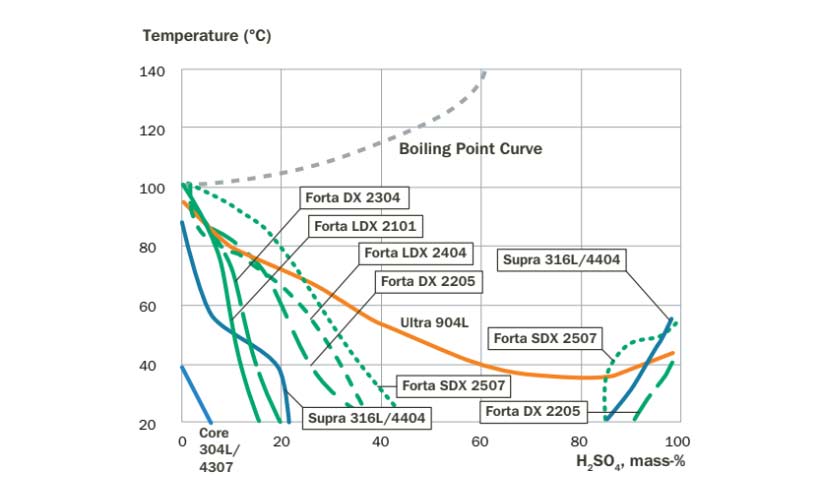
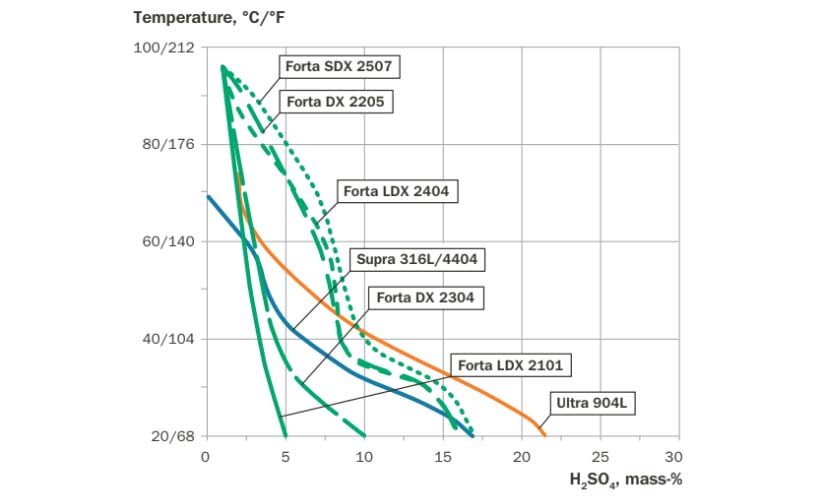
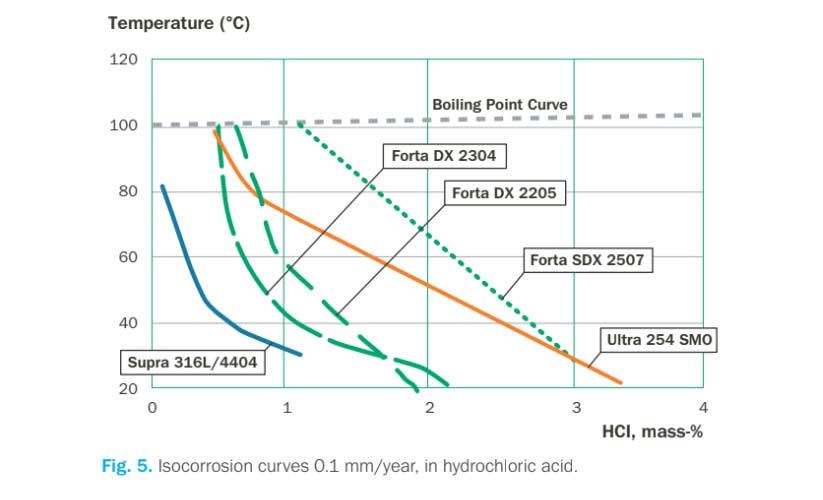
- Uniform Corrosion: Due to high chromium content, these steels resist uniform corrosion well, typically less than 0.1 mm/year.
- Sulfuric Acid: DX 2205 shows superior resistance in sulfuric acid contaminated by chloride ions compared to Supra 316L/4404.
- Hydrochloric Acid: SDX 2507 and DX 2205 can be used in dilute hydrochloric acid, with potential risks of localized corrosion in crevices.
- Nitric Acid: LDX 2101 and DX 2304, with their high chromium content and low molybdenum, are suitable for environments where resistance to strongly oxidizing nitric acid is needed.
PRE values for Forta Duplex grades and some austenitic grades
Steel designations |
PRE |
|||
name | EN | ASTM Type |
UNS | |
2205 | 1.4462 | 2205 | S32205 | 35 |
2507 | 1.4410 | 2507 | S32750 | 43 |
Results from stress corrosion cracking immersion tests in chloride solutions
name | ASTM G123 | ASTM G36 | ||
25% NaCl, pH 1.5, 106°C (b.p.), 1,000 h | 40% CaCl2, 100°C, 500 h | 45% MgCl2, 155°C (b.p.), 24 h | ||
U-bend samples | 4-PB samples (90% of Rp0.2) | U-bend samples | ||
2205 | No SCC | No SCC | SCC | |
2507 | No SCC | No SCC | SCC |
Mechanical properties according to EN 10088 and EN 10028
EN | ASTM | Product form | Yield strength | Tensile | Elongation | Elongation | |
name | UNS | Rp0.2[MPa] | strength | A[%] | A80[%] | ||
Rm[MPa] | |||||||
2205 | 1.4462 | S32205 | Cold rolled coil (C) | 500 | 700–950 | 20 | 20 |
Hot rolled coil (H) | 460 | 700–950 | 25 | 25 | |||
Quarto plate (P) | 460 | 640–840 | 25 | 25 | |||
Wire rod 1) | 510 | 750 | 35 | – | |||
Bar | 450 | 650–880 | 25 | – | |||
2507 | 1.4410 | S32750 | Cold rolled coil (C) | 550 | 750–1000 | 20 | 20 |
Hot rolled coil (H) | 530 | 750–1000 | 20 | 20 | |||
Quarto plate (P) | 530 | 730–930 | 20 | 20 | |||
Bar | 530 | 730–930 | 25 | – | |||
1.4510 | S32760 | Cold rolled coil (C) | 550 | 750–1000 | 20 | 20 | |
Hot rolled coil (H) | 530 | 750–1000 | 25 | 25 | |||
Quarto plate (P) | 530 | 730–930 | 25 | 25 |
Mechanical properties according to ASTM A240
EN | ASTM | Product form | Yield | Yield | Tensile | Tensile | Elongation | |
name | UNS | strength | strength | strength | strength | A50[%] | ||
Rp0.2[MPa] | Rp0.2 [ksi] | Rm [MPa] | Rm [ksi] | |||||
2205 | 1.4462 | S32205 | Plate, sheet and strip | 450 | 65 | 655 | 95 | 25 |
Wire rod 1) | 510 | 74 | 752 | 109 | – | |||
2507 | 1.4410 | S32750 | Plate, sheet and strip | 550 | 80 | 795 | 116 | 15 |
100 | 1.4501 | S32760 | Plate, sheet and strip | 550 | 80 | 750 | 108 | 25 |
Mechanical properties at elevated temperatures, minimum yield strength according to EN 10028-7
name | Strength | 100°C | 150°C | 200°C | 250°C | |
2205 | Yield strength | Rp0.2 [MPa] | 360 | 335 | 315 | 300 |
Tensile strength | Rm [MPa] | 590 | 570 | 550 | 540 | |
2507 | Tensile strength | Rm [MPa] | 680 | 660 | 640 | 630 |
Physical properties
Metric values according to EN 10088-1
name | EN | ASTM Type | UNS | Density [kg/dm3] | Modulus of elasticity at 20°C [GPa] | Coefficient of thermal expansion 20–100°C [10-6/K] | Thermal conductivity at 20°C [W/(m x K)] | Thermal capacity at 20°C [J/(kg x K)] | Electrical resistivity at 20°C [Ω x mm2/m] |
2205 | 1.4462 | 2205 | S32205 | 7.8 | 200 | 13.0 | 15 | 500 | 0.8 |
2507 | 1.4410 | 2507 | S32750 | 7.8 | 200 | 13.0 | 15 | 500 | 0.8 |
100 | 1.4410 | - | S32760 | 7.8 | 200 | 13.0 | 15 | 500 | 0.8 |
Imperial values converted from Table 10
name | Density [lbm/in3] | Modulus of elasticity [psi] | Coefficient of thermal expansion 68–212°F [μin / (in x °F)] | Thermal conductivity [Btu/(hr x ft x °F)] | Thermal capacity [Btu/(lbm x °F)] | Electrical resistivity [μΩ x in] |
2205 | 0.282 | 29 x 106 | 7.2 | 8.7 | 0.119 | 31.50 |
2507 | 0.282 | 29 x 106 | 7.2 | 8.7 | 0.119 | 31.50 |
Fabrication
Duplex stainless steel is suitable for all forming processes used for stainless steel. The high yield strength compared to austenitic and ferritic stainless steel can however give differences in forming behavior. Depending on the chosen forming technique there could be consequences, such as increased springback. This point is particularly relevant to the forming of any high strength steel. Moreover, an excellent interplay between high yield strength, work hardening rate and elongation promote the duplex grades for light weight and cost-efficient applications with complex shapes. The impact of the high strength varies for different forming techniques. Common for all is that the estimated forming forces will be higher than for the corresponding austenitic and ferritic stainless steel grades. This effect will usually be lower than expected from just the increase in strength since the choice of duplex stainless steel is often associated with gauge reduction. It is important to consider that duplex stainless steel may also be more demanding on the tools and on the lubricant. This should also be noted when looking to down gauge.
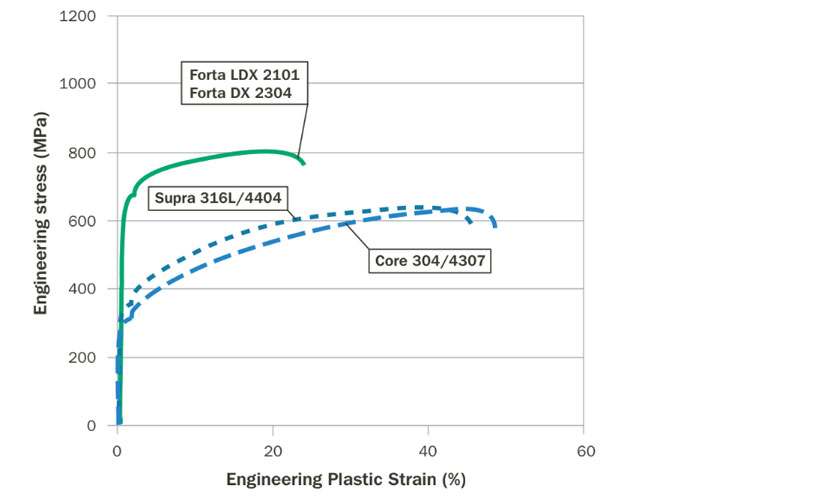
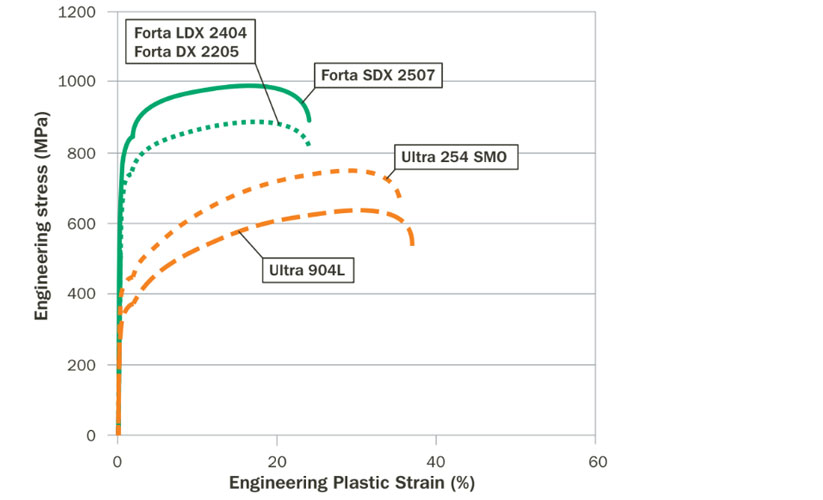
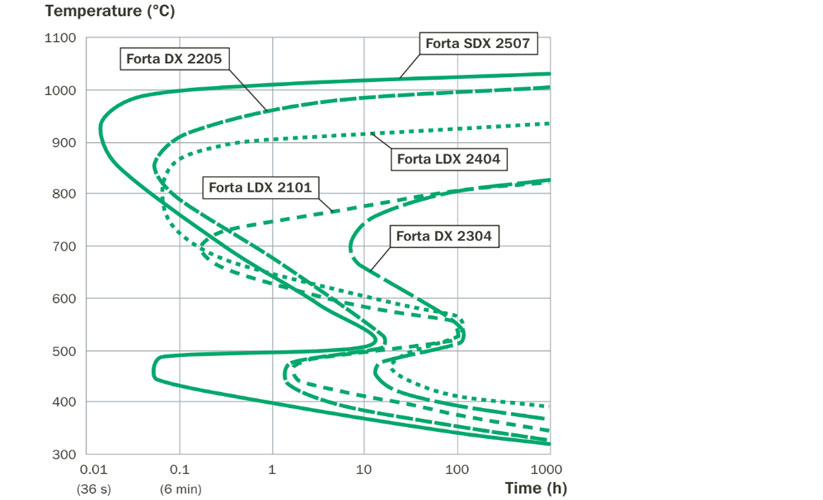
Welding consumables
name | EN | ASTM Type | UNS | Consumable ISO designation |
2507 | 1.4462 | 2205 | S32205 | 22 9 3 NL |
2507 | 1.4410 | 2507 | S32750 | 25 9 4 NL |
General characteristics
Steel designations |
Performance |
Typical chemical composition, % by mass |
||||||||||
name |
EN |
ASTM |
UNS |
PRE |
A1) |
Rp0.2 |
Grade |
C |
Cr |
Ni |
Mo |
N |
2205 | 1.4462 | 2205 | S32205 | 35 | 20 | 500 | D | 0.02 | 22.4 | 5.7 | 3.1 | 0.17 |
2507 | 1.4410 | 2507 | S32750 | 43 | 20 | 550 | D | 0.02 | 25.0 | 7.0 | 4.0 | 0.27 |
Product
Quick contact
Get Solution
Organically grow the holistic world view of disruptive innovation via workplace diversity
Contact Us